What is a bill of materials (BOM)?
A Bill of Materials (BOM) is an essential document used in the manufacturing process. It outlines all the components, raw materials, subassemblies, and parts required to produce a finished product. Along with listing each item, a BOM typically includes important details such as the quantity needed, part numbers, item descriptions, units of measure, and sometimes even supplier information or sourcing type.
There are various types of BOMs depending on the use case. For instance, an Engineering BOM (EBOM) is generated during the product design phase and reflects how the product is conceptually structured. A Manufacturing BOM (MBOM), on the other hand, is tailored for production needs and includes all items necessary for manufacturing, including packaging. Other variants like the Sales BOM (SBOM) and Service BOM serve different roles—such as defining sales kits or listing parts for product maintenance and repair.
BOMs are crucial to many aspects of production and supply chain management. They help ensure that products are assembled correctly and efficiently while also supporting accurate inventory tracking, cost control, and procurement planning. Moreover, a well-maintained BOM enhances product traceability and compliance, making it a critical tool for both engineers and manufacturers.
Why BOM Management Matters
Electronics manufacturing involves intricate processes that rely on the accuracy, clarity, and accessibility of the BOM. The BOM serves as the foundational document that links product design, procurement, assembly, and support functions. A poorly managed BOM can result in production delays, sourcing difficulties, increased exposure to counterfeit electronic components, and non-compliance with industry standards.
With the globalization of the electronics supply chain and the rise in demand for customized, high-quality products, the need for robust BOM management practices has never been greater. Electronics manufacturers who master BOM management can reduce costs, improve time-to-market, enhance product quality, and maintain a competitive edge.
What is an Electronic BOM?
An electronic BOM, or Bill of Materials, is a comprehensive list of all the components, parts, raw materials, and subassemblies needed to manufacture an electronic product. It includes critical details such as part numbers, quantities, descriptions, manufacturer names, reference designators, lifecycle status, and sourcing alternatives. BOMs can vary in complexity from a few components for a simple PCB to thousands of items for a multi-board assembly.
Types of BOMs:
There are several types of BOMs used throughout the electronics product lifecycle:
• Engineering BOM (EBOM): Created during the product design phase and focuses on functional components.
• Manufacturing BOM (MBOM): Tailored for production and includes all items required for manufacturing, including packaging materials.
• Service BOM (SBOM): Used for maintenance and repair and includes components subject to wear and failure.
Each BOM type must be carefully managed to ensure consistency and alignment across engineering, procurement, and manufacturing teams.
Challenges in Electronics BOM Management
Creating a bill of materials (BOM) is just the beginning of its journey. In electronics manufacturing, BOM management extends throughout the product’s entire lifecycle. BOM management in electronics is fraught with challenges that can affect product quality, cost, and delivery timelines. Managing a Bill of Materials (BOM) in the electronics industry can be particularly challenging due to the complexity, rapid pace of innovation, and supply chain dynamics. Here are the key challenges electronics manufacturers and OEMs face in BOM management:
1. Component Shortages and Volatile Lead Times
The global electronics supply chain is highly sensitive to geopolitical tensions, natural disasters, and fluctuations in demand. This can lead to unpredictable lead times and component shortages. BOM managers must anticipate disruptions and maintain flexibility through proactive sourcing and alternative component strategies.
2. Counterfeit Electronic Components
The rise in counterfeit electronics, particularly during periods of scarcity, poses a significant threat to manufacturers. Counterfeit components can compromise product performance, safety, and brand reputation. BOMs must include traceable, verified components sourced from authorized distributors to minimize risk.
3. Multi-Site Collaboration and Data Consistency
Many electronics manufacturers operate across multiple locations. Ensuring consistency in BOM data across geographically dispersed teams is challenging but essential. A lack of version control and centralized access can lead to miscommunication, errors, and increased operational costs.
4. Component Obsolescence and Lifecycle Management
Technological innovation in the electronic industry often leads to shorter component lifecycles. BOMs must be continuously updated with lifecycle data to prevent the use of obsolete components. Failure to manage obsolescence can halt production and increase redesign costs.
Best Practices for BOM Management
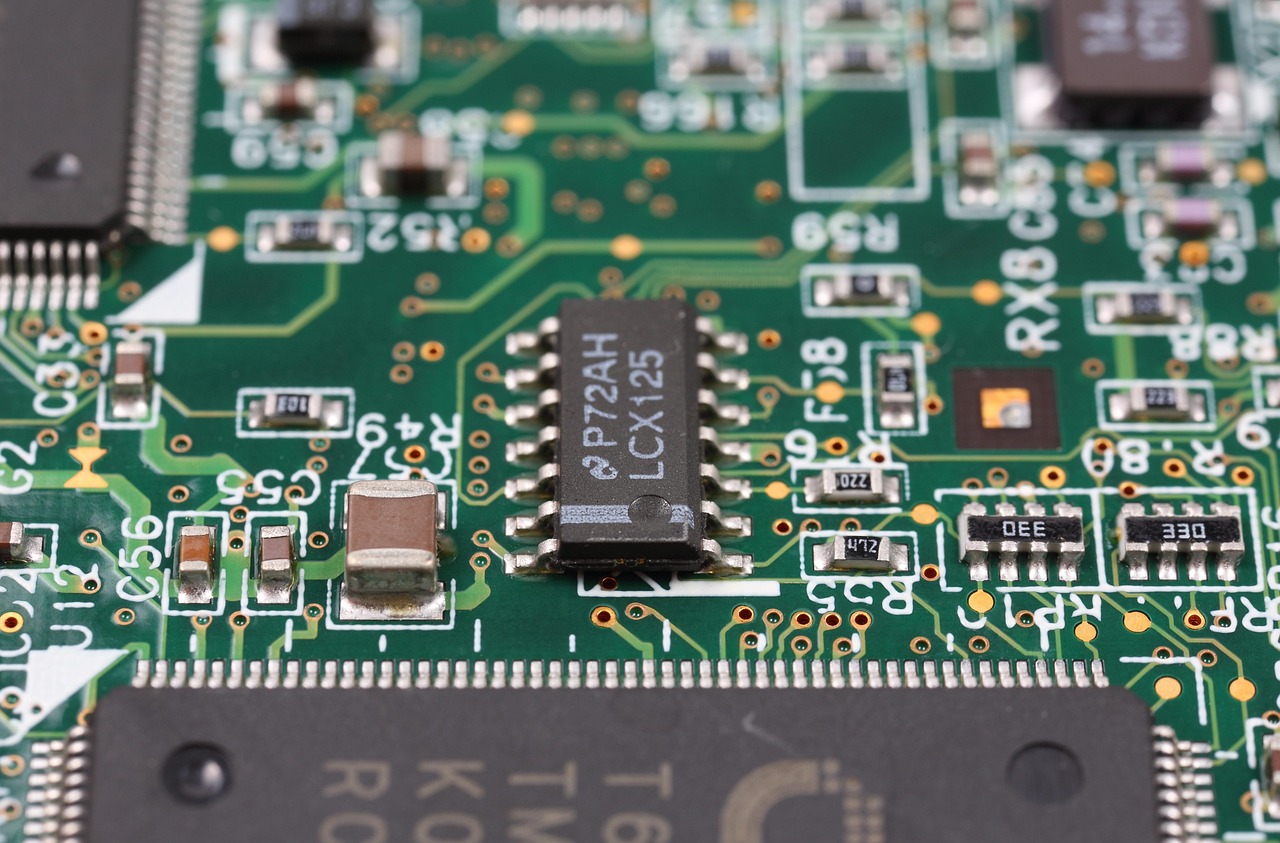
• Centralize BOM Data in the Cloud
Centralized, cloud-based BOM systems ensure that all stakeholders, including design, procurement, and production teams, have access to a single source of truth. This reduces errors, enhances collaboration, and facilitates real-time updates.
• Include Alternative and Substitute Parts
Listing qualified alternative components in the BOM provides flexibility in sourcing and helps mitigate supply disruptions. It allows electronic buyers to quickly pivot to in-stock or locally available components without redesigning the product.
• Monitor Lifecycle and Compliance Status
BOMs should integrate real-time lifecycle and compliance data. Tools that pull information from electronic component news sources and global compliance databases help ensure components meet regulatory standards like RoHS and REACH.
• Integrate BOMs with ERP and PLM Systems
Seamless integration of BOMs with Enterprise Resource Planning (ERP) and Product Lifecycle Management (PLM) systems promotes synchronization between design, procurement, and inventory systems. This integration supports better forecasting, inventory control, and production planning.
• Implement Robust Version Control
Track and document all changes to the BOM throughout the product lifecycle. Version control ensures transparency, traceability, and accountability, which is critical during audits and product revisions.
• Validate Manufacturer Part Numbers and Sources
Ensuring that part numbers and manufacturer details are accurate reduces procurement errors and enhances sourcing reliability. Verified data helps detect and prevent counterfeit electronic components.
• Collaborate with Trusted Suppliers
Partnering with reputable suppliers and distributors who prioritize transparency, compliance, and traceability is essential. Suppliers that offer electronic component sourcing tools, API access, and authentication services can be valuable allies in maintaining BOM integrity.
BOM Software Platforms Comparison
Here’s a comparison of popular BOM software platforms used by electronics manufacturers, OEMs, and supply chain professionals. These platforms help manage BOM complexity, ensure data accuracy, and integrate with design, ERP, and procurement systems.
Feature / Platform | Arena PLM | Altium 365 | SiliconExpert | BOMCheck | Octopart + Upverter |
---|---|---|---|---|---|
Cloud-Based Access | Yes | Yes | Yes | Yes | Yes |
Lifecycle Status Monitoring | Yes | Yes | Yes | Yes | Yes |
Compliance Data (RoHS/REACH) | Yes | No | Yes | Yes | Yes |
Collaboration Tools | Yes | Yes | Limited | Yes | Yes |
Supplier Integration | Yes | Yes | Yes | No | Yes |
Cost Estimation | Yes | Yes | Yes | No | Yes |
Counterfeit Risk Mitigation | Yes | No | Yes | Yes | Yes |
Ideal for SMEs | Yes | Yes | No | Yes | Yes |
Role of BOMs in the Electronics Supply Chain
The BOM is the connective tissue of the electronics supply chain, linking design, sourcing, production, and logistics. It guides electronic buyers in planning purchases, helps logistics teams manage inventory, and provides production lines with a clear materials roadmap. BOMs are also crucial for traceability and quality assurance, especially in high-reliability sectors like aerospace and medical electronics.
The Bill of Materials (BOM) plays a pivotal role in the electronics supply chain, acting as the central document that connects design, sourcing, production, and delivery processes. It serves not just as a product blueprint, but also as a strategic tool for managing inventory, procurement, compliance, and costs throughout the product lifecycle. By maintaining a detailed and accurate BOM, manufacturers can reduce procurement errors, prevent the use of counterfeit electronics, and ensure alignment across all departments and locations involved in electronics production.
Avoiding Counterfeit Electronics Through BOM Control
Avoiding counterfeit electronics is a major concern for OEMs, manufacturers, and distributors—especially as global supply chains become more complex and fragmented. A well-managed BOM (Bill of Materials) plays a crucial role in detecting and preventing the entry of counterfeit or substandard components into the supply chain. Counterfeit electronic components continue to plague the industry, especially when supply chains are stressed. To mitigate this risk, manufacturers should:
• Source components exclusively from franchised or authorized distributors.
• Utilize third-party verification and authentication services.
• Integrate serialization and traceability data into the BOM.
• Regularly monitor component news for counterfeit alerts.
• Conduct physical and functional testing of critical components.
These practices, when embedded into BOM management workflows, significantly enhance product reliability and protect brand reputation.
Future Trends in BOM Management
The future of BOM (Bill of Materials) management in the electronics industry is evolving rapidly, driven by digitization, globalization, and the increasing complexity of supply chains. Here are the top trends shaping the future of BOM management and how they will impact manufacturers, OEMs, and distributors:
• Artificial Intelligence and Predictive Analytics
AI-powered tools can analyze historical data and current trends to predict which components are at risk of obsolescence or supply disruptions. This enables proactive planning and strategic sourcing.
• Smart BOMs Connected to Live Market Data
Next-generation BOMs are increasingly linked to real-time component availability, pricing, and news feeds. These smart BOMs automatically suggest alternatives and update lifecycle status without manual intervention.
• Blockchain for Secure Traceability
Blockchain technology is being explored to create immutable records of BOM changes, supplier interactions, and component provenance. This enhances trust, traceability, and accountability in the electronics distribution chain.
• API Integration with Distributors and Marketplaces
Modern BOM tools offer APIs that connect directly with electronic distribution platforms, enabling automatic sourcing, quoting, and compliance checks. This reduces lead times and manual data entry.
FAQ: BOM Management for Electronics
1. What is a BOM in electronics?
A Bill of Materials (BOM) in electronics is a detailed list of every component and part required to manufacture an electronic product. It serves as the blueprint for procurement, production, and maintenance.
2. How does BOM management affect the electronics supply chain?
Effective BOM management ensures that all stakeholders have access to accurate, current component data. This improves sourcing accuracy, production efficiency, and risk mitigation across the electronics supply chain.
3. How do I choose the best BOM software?
Choose a platform that supports your organization’s scale, integrates with your existing ERP/PLM systems, provides real-time compliance data, and offers tools to detect counterfeit risks.
4. What are common errors in BOMs?
Frequent mistakes include outdated lifecycle information, incorrect part numbers, missing compliance documentation, and lack of substitute components. These errors can lead to sourcing delays and increased costs.
5. What role does BOM play in electronic component sourcing?
The BOM guides procurement teams in sourcing the correct components by specifying part numbers, approved manufacturers, and acceptable alternates. A well-managed BOM reduces sourcing risks and improves supplier collaboration.
Final Thoughts
In a complex and competitive marketplace, mastering BOM management is essential for success in the electronics manufacturing services market. A strategic, proactive approach to BOMs not only optimizes production and sourcing but also protects against disruptions and counterfeit threats.
As the industry continues to evolve, staying informed through trusted electronic design news and adopting cutting-edge BOM management tools will be key differentiators for manufacturers aiming for excellence in quality, speed, and innovation. For continuous updates and expert insights, follow our electronics blog and stay ahead of the latest trends in consumer electronics news and electronic components news.
Read More:
• The Evolution of Semiconductor Manufacturing: From Transistors to Integrated Circuits
• Electronic Contract Manufacturing: The Backbone of Modern Electronics Production
• What is an Electronic Component Broker?
Written by Jack Zhang from AIChipLink.
AIChipLink, one of the fastest-growing global independent electronic component distributors in the world, offers millions of products from thousands of manufacturers, and many of our in-stock parts is available to ship same day.
We mainly source and distribute integrated circuit (IC) products of brands such as Broadcom, Microchip, Texas Instruments, Infineon, NXP, Analog Devices, Qualcomm, Intel, etc., which are widely used in communication & network, telecom, industrial control, new energy and automotive electronics.
Empowered by AI, Linked to the Future. Get started on AIChipLink.com and submit your RFQ online today!